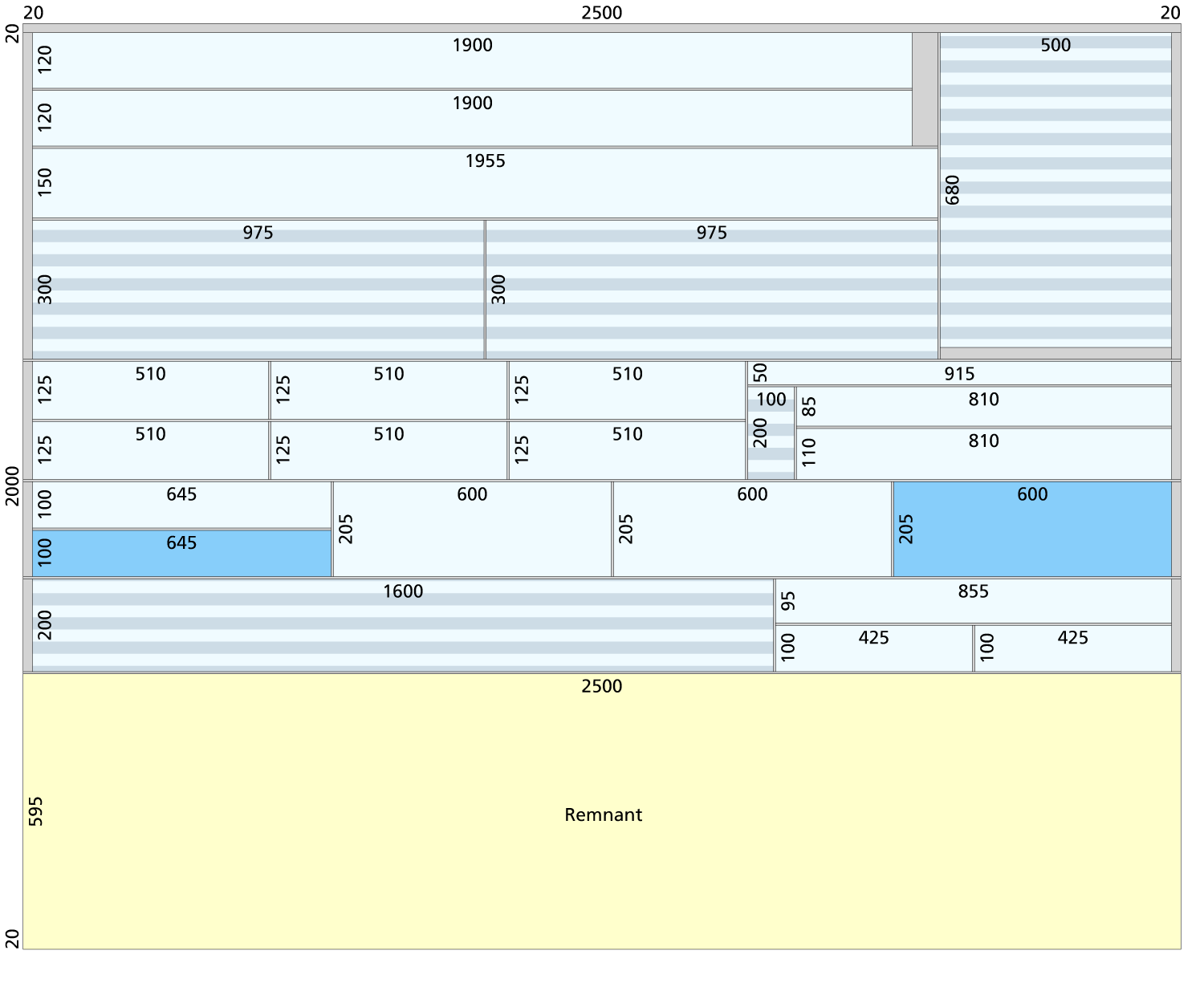
The AutoPanelSizer software generates optimized cutting layouts for the production of rectangular parts from rectangular raw materials, minimizing waste, production time, and manufacturing costs. The resulting cutting layouts are based on straight, end-to-end guillotine cuts. This makes AutoPanelSizer ideal for use with common sawing technologies in the wood industry as well as in glass, metal, and plastics processing.
Cutting layouts in seconds
AutoPanelSizer can compute layouts with an adjustable number of cutting stages, allowing for a flexible adjustment of the nesting depth. The software supports head cuts and recuts, and considers various constraints imposed by the cutting process and the material. This makes AutoPanelSizer suitable for both highly automated industrial sawing lines with a limited number of cutting stages, as well as panel dividing saws that can cut highly nested layouts. The optimization can include available remnants and raw boards of different sizes. The computation of a typically sized cutting layout takes only a few seconds to a couple of minutes and can be sped up using multiple processor cores.